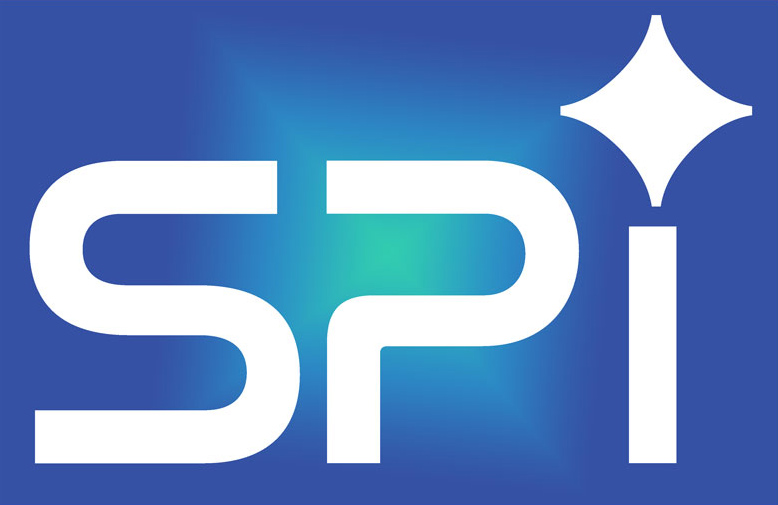
Steel Performance Initiative
SPI organizes collaboration between steel industry leaders and university researchers led by the Steel Founders’ Society of America (SFSA) to answer the DoD’s call for innovation. Defense needs have transitioned from asymmetric conflicts with terrorists to preparing for peer-to-peer confrontations. This highlights the need for higher performance capability of steel components in weapon systems.
For decades the development and deployment of new steel technologies has been under-supported. Investing in the industrial base positions the US as commercial leaders while improving legacy weapon systems support, providing state-of-the-art protection for the warfighter, and preparing for the next generation of DoD needs. Strategic steel initiatives have been identified for research vital to support current and future defense objectives.
SPI invests in defining best practices, alloy development, and manufacturing technology so that the U.S. remains the leading world power in both defense and industry steel technology. SPI research thrusts will:
- Improve MRL and TRL of Advanced High Strength Steels (AHSS) for weapon system transition.
- Develop process-driven performance modeling methodology supported by robust datasets to enable Fitness for Purpose (FFP) designs.
- Formulate quantitative nondestructive testing (QNDT) methods and standards based on part performance.
- Tailor Industry 4.0 technology for short-run steel production in Small and Medium Enterprises (SME).
- Couple manufacturing processes for hybrid capability and optimize to create unique geometry, superior properties or cost-effective solutions.
- Mine properties of existing materials from published data and interrogate with smart analytics for improved alloys, modeling and design properties.
- Provide a guide for the use of current specifications as alternatives to obsolete requirements of parts in legacy weapon systems.
- Enable predictable blast and ballistic performance from high strain rate data with microstructural correlation.